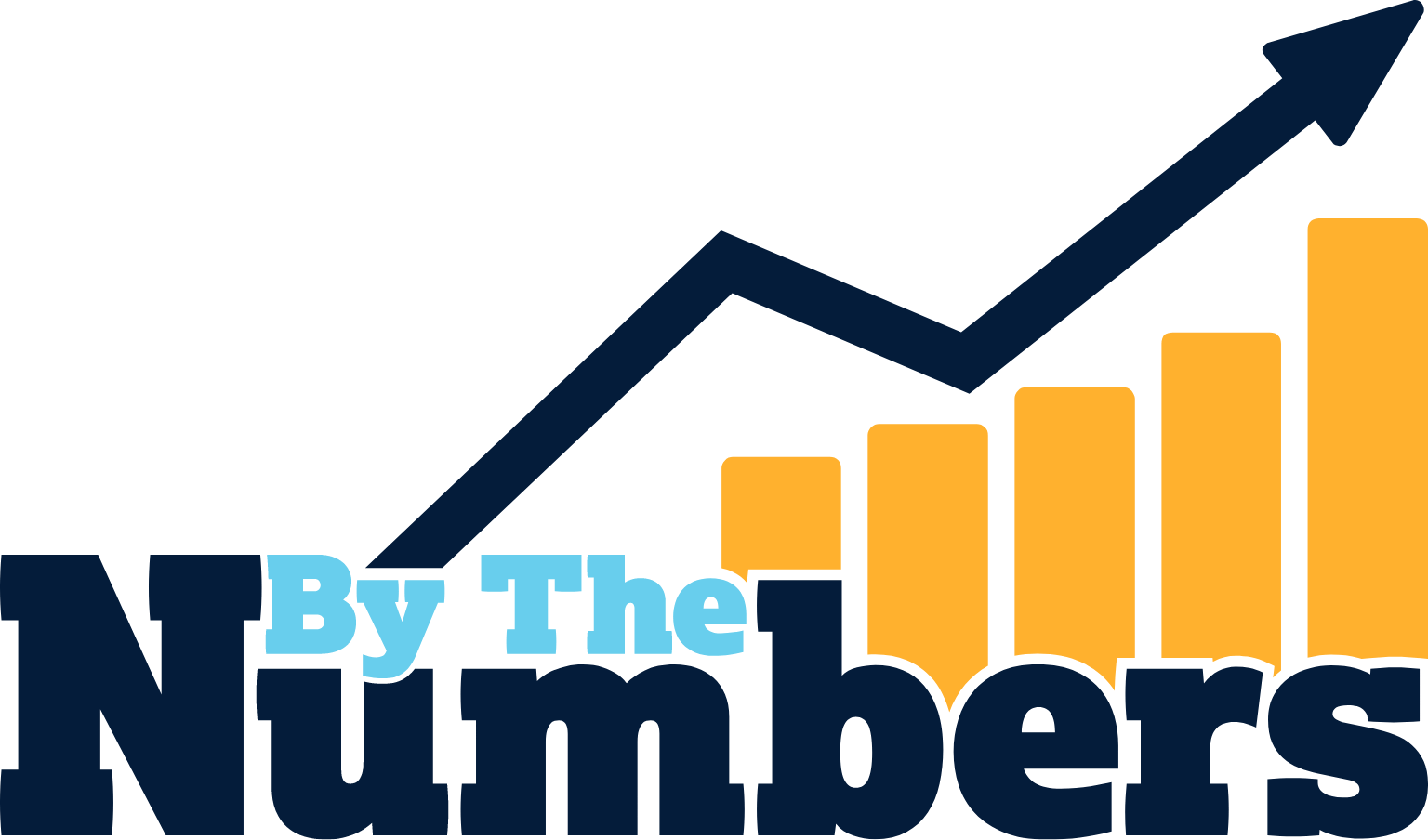
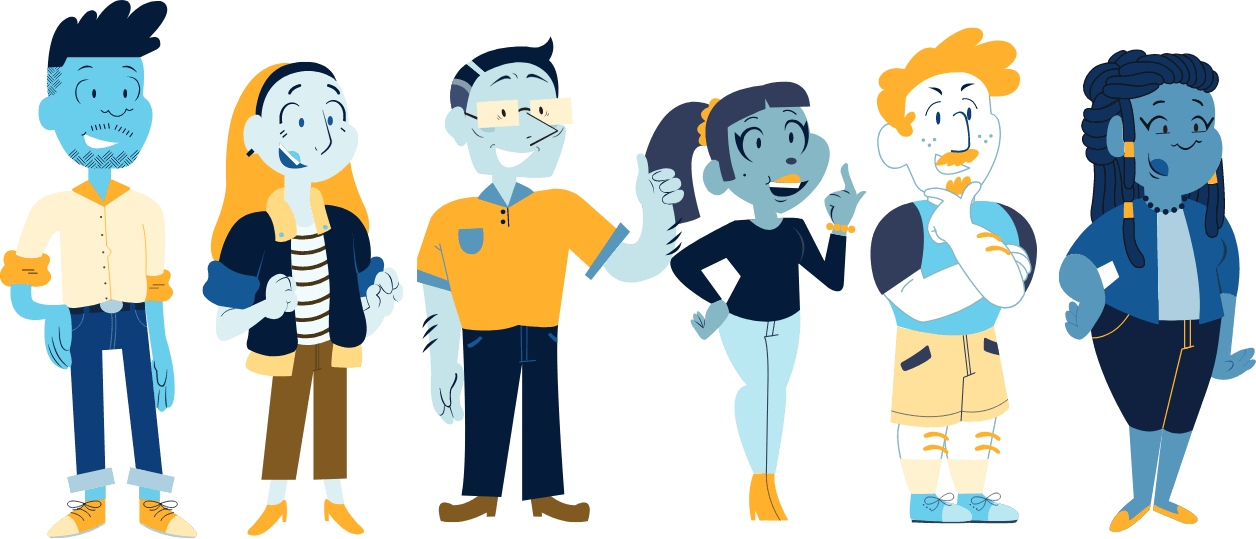
American Workers Are Quitting — Especially in the Manufacturing Industry
Across the nation, quit rates have skyrocketed in the aftermath of 2020.
This has posed a huge challenge for employers across industries.
Quits: Total Nonfarm
Source: Bureau of Labor Statistics
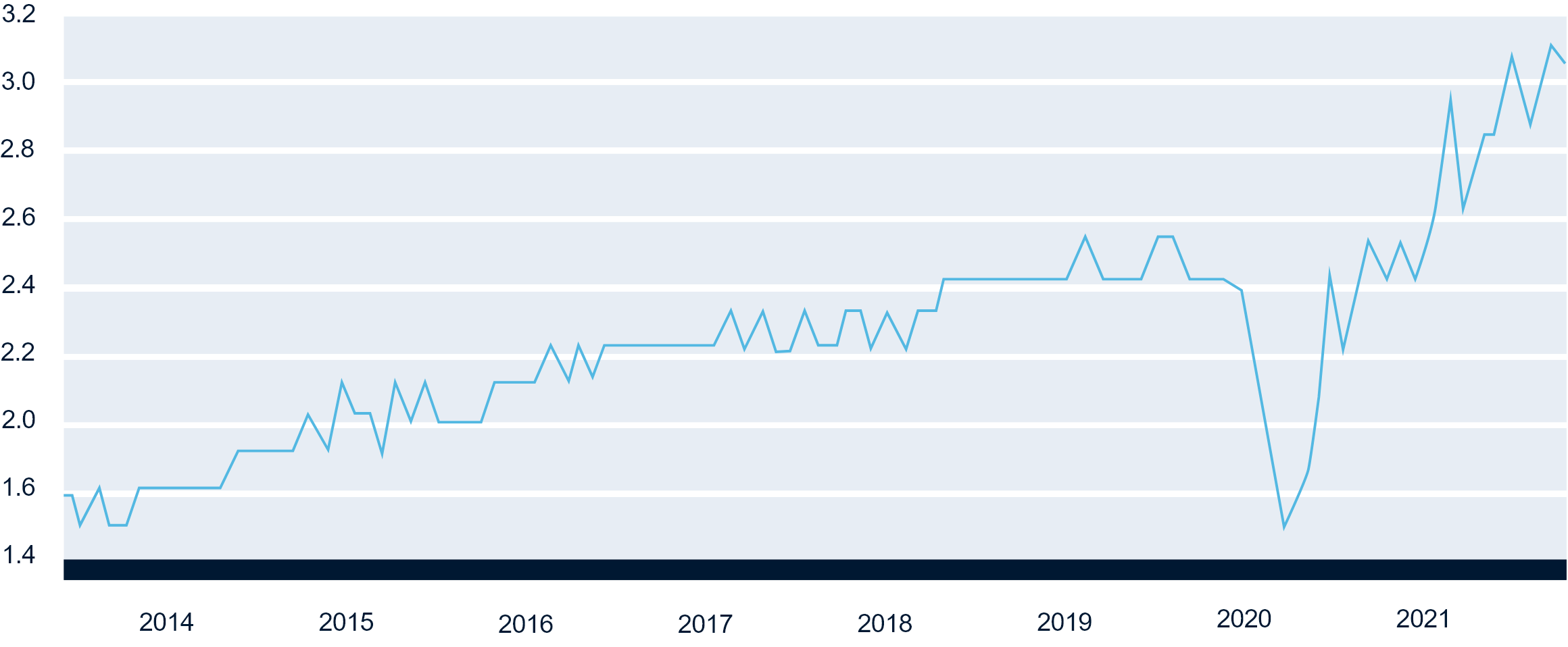
That said, manufacturing has been hit especially hard by what is being called the great resignation. Quit rates in the manufacturing sector have soared, significantly outpacing other industries. This has left many in the manufacturing and manufacturing-adjacent industries struggling to meet production while those remaining deal with increasingly high levels of burnout.
As manufacturing companies deal with increasingly high turnover rates, many understand that this level of turnover is likely to continue through 2022 and beyond. Left unaddressed, this level of turnover is both destructive and unsustainable.
That leads us to an important question: How can the manufacturing industry decrease its turnover rate, improve its recruiting efforts, and start building more sustainable teams?
To understand the options, we must first understand employees perspectives to determine what barriers in manufacturing are causing employees to leave their jobs. By understanding the needs of the modern employee, we can update our work environments so they work for everyone.
Percent Change in Quits Level
Late 2021 vs. Pre-Pandemic
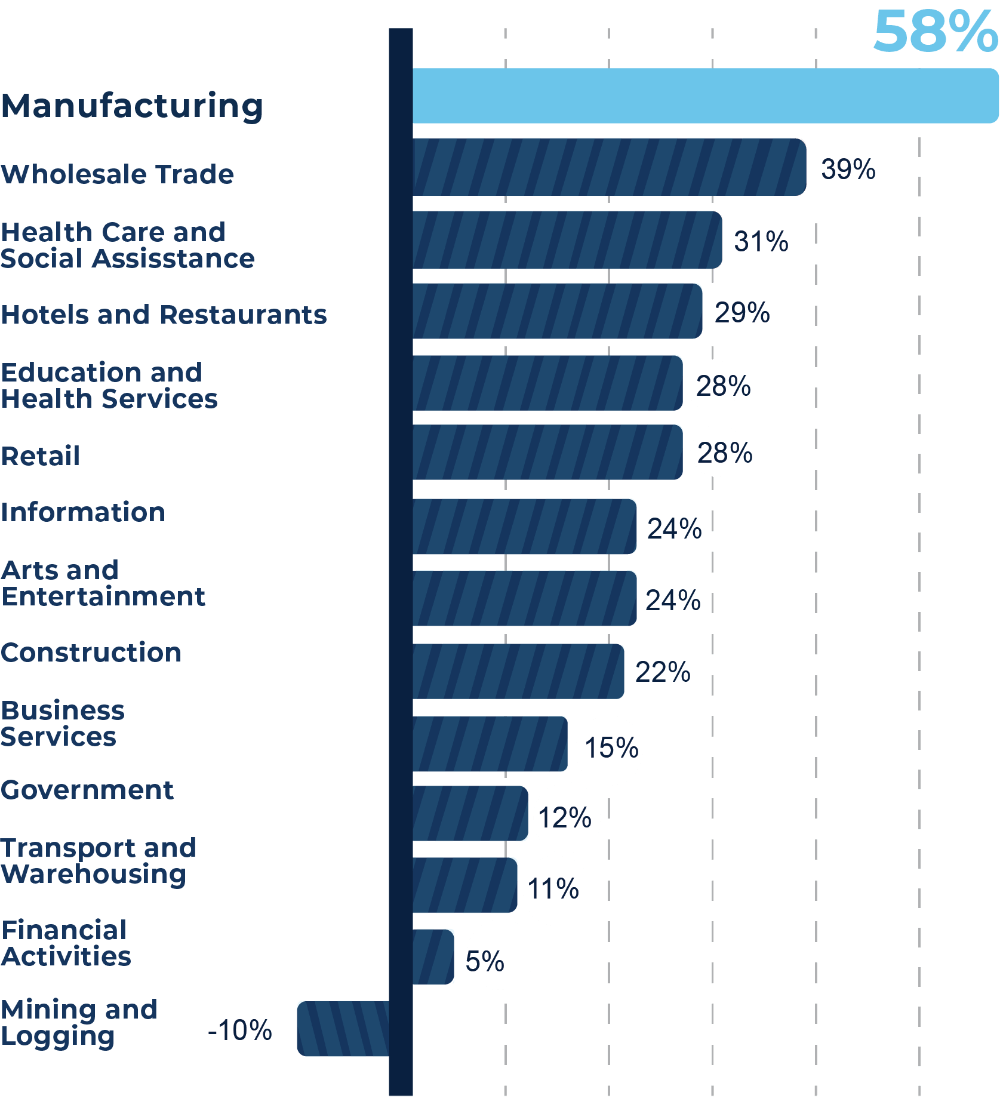
Source: Bureau of Labor Statistics
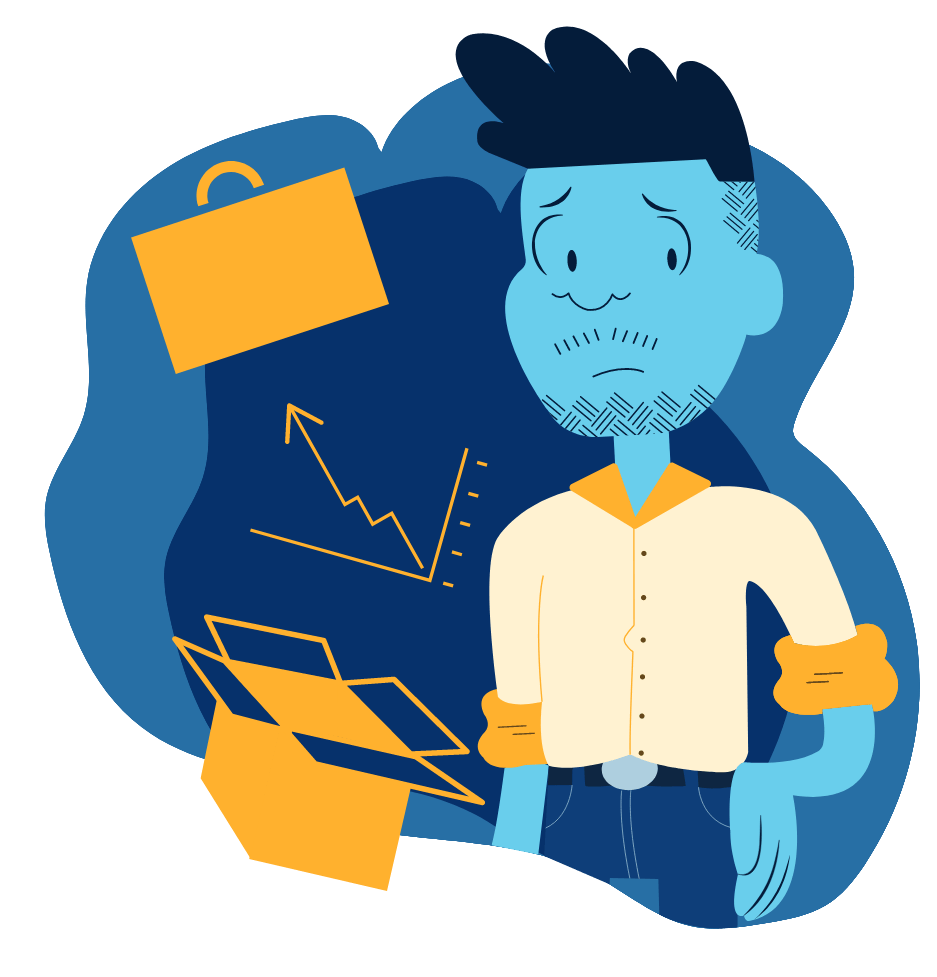
Jayden needs a paycheck that keeps up with inflation.
Jayden is 25-years-old and has an associate’s degree. He works as a production associate and makes $15.00 per hour. He likes his job and doesn’t want to leave. The problem is, the cost of rent in his city is skyrocketing, and Jayden’s wages just aren’t cutting it anymore, even with the raise he was recently given. Jayden knows other industries are offering more money for his skill set. Jayden decides to put his associate’s degree to use and find a job that pays more and will allow him to afford his current apartment. Within a week, Jayden has accepted a new job making $18.50 per hour with benefits as an entry-level accounts receivable specialist. He doesn’t love working at a desk job all day and misses the active life of a manufacturing plant, but Jayden knows he has made the best decision for his financial future.
Jayden needs a paycheck that keeps up with inflation.
Jayden is 25-years-old and has an associate’s degree. He works as a production associate and makes $15.00 per hour. He likes his job and doesn’t want to leave. The problem is, the cost of rent in his city is skyrocketing, and Jayden’s wages just aren’t cutting it anymore, even with the raise he was recently given. Jayden knows other industries are offering more money for his skill set. Jayden decides to put his associate’s degree to use and find a job that pays more and will allow him to afford his current apartment. Within a week, Jayden has accepted a new job making $18.50 per hour with benefits as an entry-level accounts receivable specialist. He doesn’t love working at a desk job all day and misses the active life of a manufacturing plant, but Jayden knows he has made the best decision for his financial future.
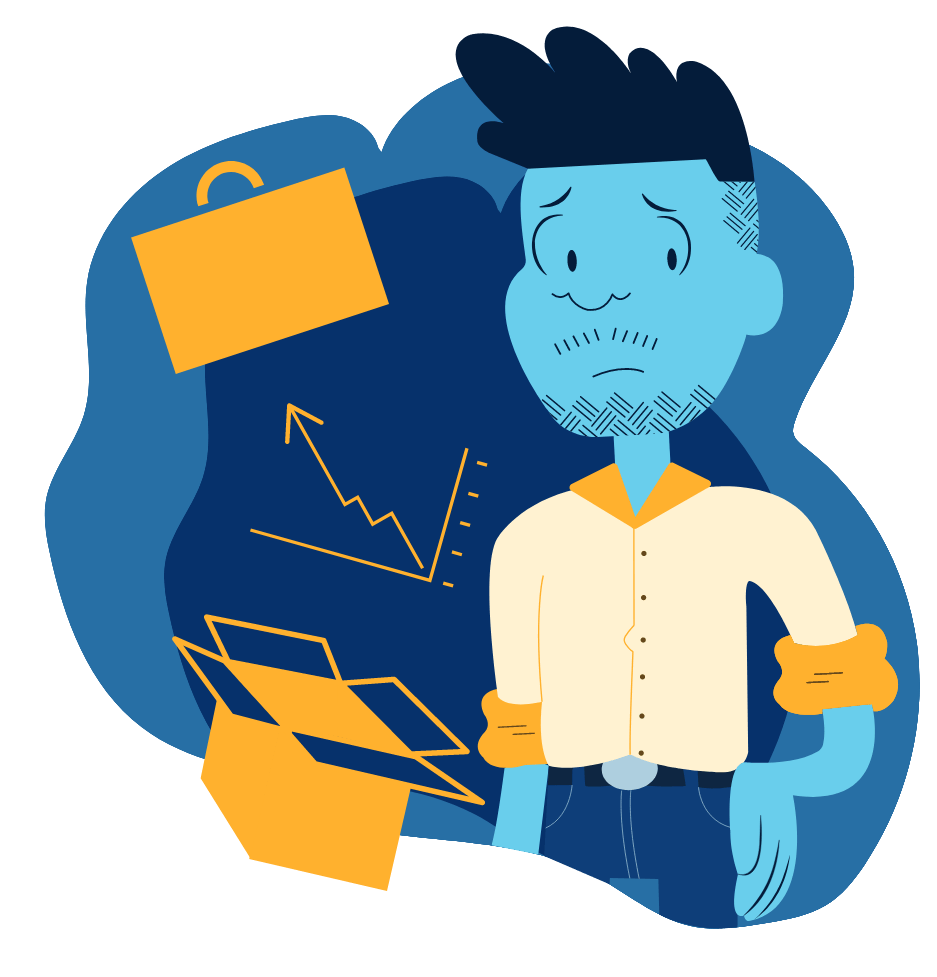
The Manufacturing Industry Offers Low Pay
For a certain generation, manufacturing was associated with the American dream — it was a job that require hardwork but provided generous compensation that allowed a worker to buy a modest home lined with a metaphoric white picket fence. Unfortunately, those days are gone in manufacturing.
From the mid-1970s to mid-2000s, the manufacturing industry offered pay for nonsupervisory workers that exceeded the average pay in other industries. Today, manufacturing offers pay that is below the average in the private sector. In fact, many manufacturing workers are considered low wage workers in today’s economy. As a result, many manufacturing workers have left the industry for higher-paying jobs in other fields.
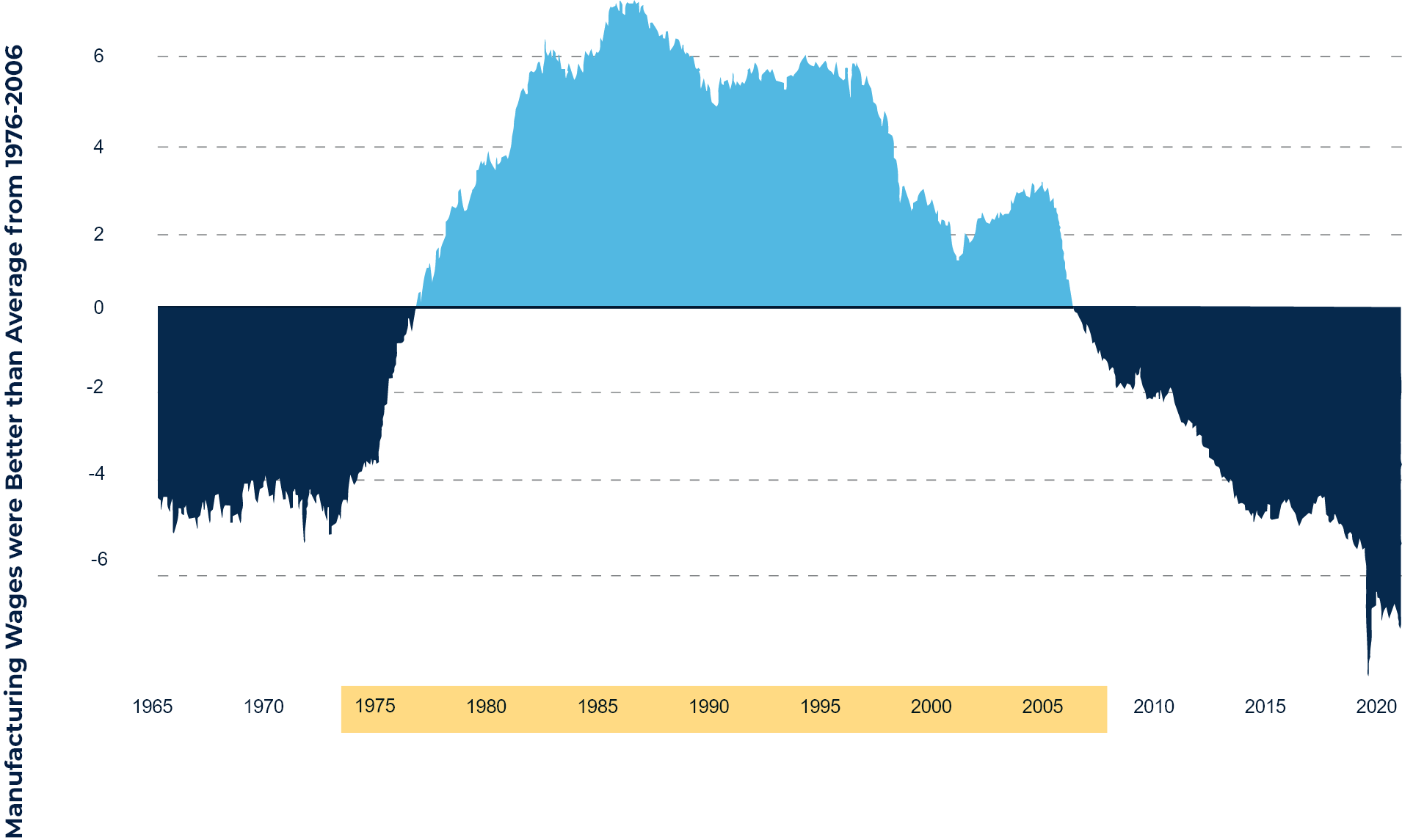
Note: Chart shows percentage that average hourly manufacturing earnings for non-supervisory workers are above or below average hourly earnings for all private-sector non-supervisory workers
Source: Bureau of Labor Statistics
Moving Forward:
Manufacturing companies need to determine how competitive their wages are within their location to ensure their employment offerings are competitive. In today’s high inflation environment, companies are competing for talent, and pay rates are changing quickly. Employers must make sure their pay rates are competitive, not only within their industry, but within their local geographic market as a whole.
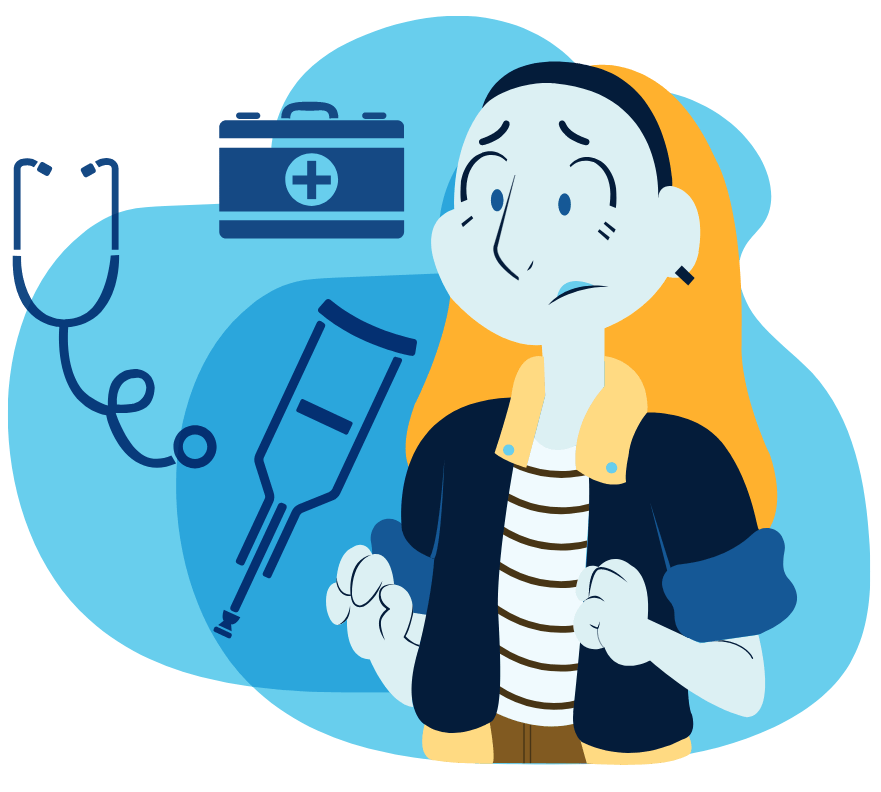
Casey needs access to affordable health insurance.
Casey is a 27-year-old woman working in a manufacturing plant who is struggling with her health. She doesn’t know what the issue is, but she can’t afford to see the doctor, so Casey keeps going about her day hoping that she will eventually feel better. The thing is, Casey actually has insurance through her employer, but because Casey lives paycheck to paycheck, she cant afford the expensive copay and deductible required to actually visit a doctor. Casey’s condition doesn’t improve, and she finds herself increasingly struggling to perform her job. Finally, Casey saves enough to go to the doctor and undergo some testing. She is diagnosed with type 1 diabetes. Because the issue went undiagnosed for so long, Casey has permanent nerve damage in her foot. Casey leaves her position and seeks to find a job that is less physically demanding and will allow her to recover and give her access to more affordable healthcare.
Casey needs access to affordable health insurance.
Casey is a 27-year-old woman working in a manufacturing plant who is struggling with her health. She doesn’t know what the issue is, but she can’t afford to see the doctor, so Casey keeps going about her day hoping that she will eventually feel better. The thing is, Casey actually has insurance through her employer, but because Casey lives paycheck to paycheck, she cant afford the expensive copay and deductible required to actually visit a doctor. Casey’s condition doesn’t improve, and she finds herself increasingly struggling to perform her job. Finally, Casey saves enough to go to the doctor and undergo some testing. She is diagnosed with type 1 diabetes. Because the issue went undiagnosed for so long, Casey has permanent nerve damage in her foot. Casey leaves her position and seeks to find a job that is less physically demanding and will allow her to recover and give her access to more affordable healthcare.
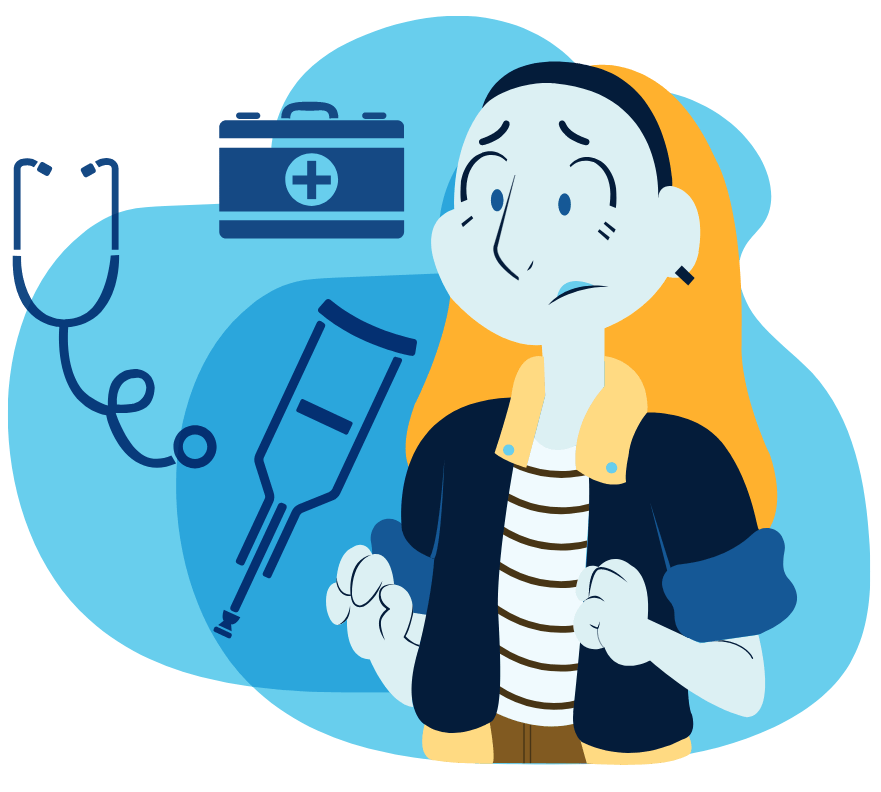
6/10
Adults in the U.S.
have a chronic disease
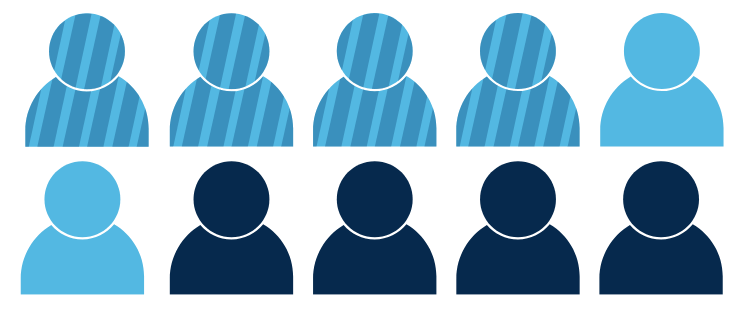
4/10
Adults in the U.S.
have two or more
chronic diseases
Workers can’t afford health insurance, which means they can’t afford to stay healthy.
In the U.S., a majority (roughly 60%) of adults have a chronic disease. At the same time, the cost of insurance has rapidly increased over the past decade, exceeding the pace of worker’s earnings. As a result, even workers with access to medical plans through their employer can oftentimes not afford to use the plans. Not having access to affordable medical insurance is a huge issue, especially for workers who have jobs that require lots of physical activity. The manufacturing industry depends on workers who are physically healthy to succeed, and ensuring these workers have access to healthcare is an important part of maintaining productive teams.
Moving Forward:
Having a healthy workforce is crucial in the manufacturing and light industrial industries. Employers should either seek to provide insurance that is affordable to their workers or partner with a company (like Ōnin) that can provide affordable benefits to workers.
Employer Premiums and Deductibles Have Risen Much Faster than Wages Since 2010
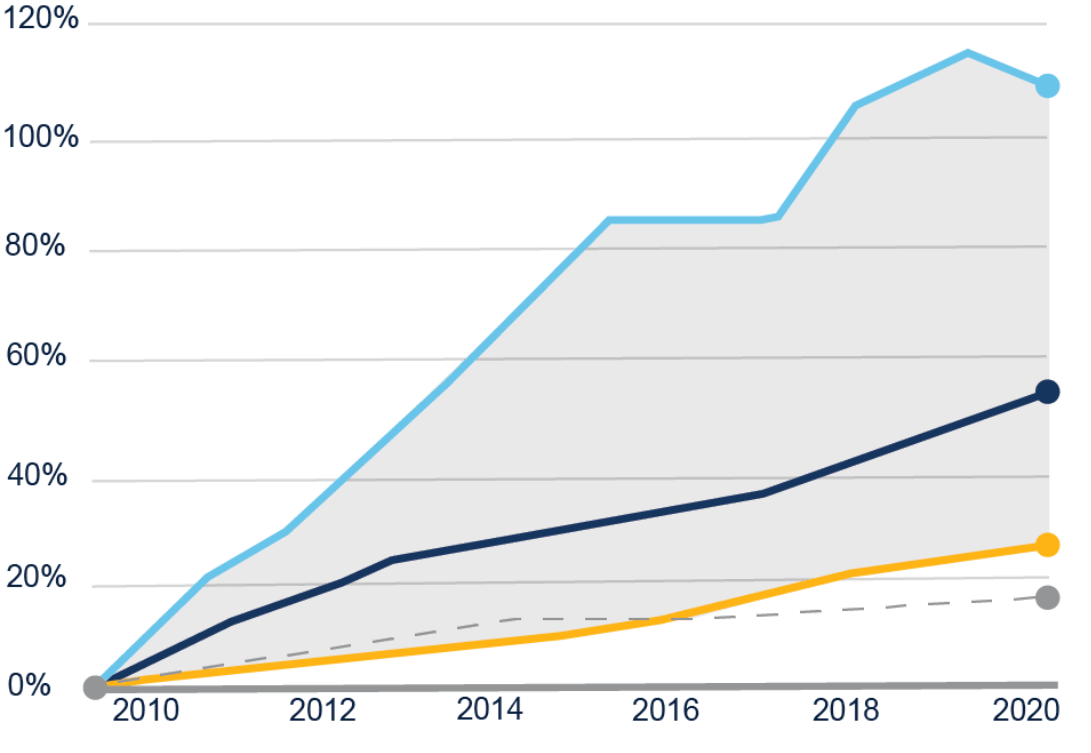
Source: KFF
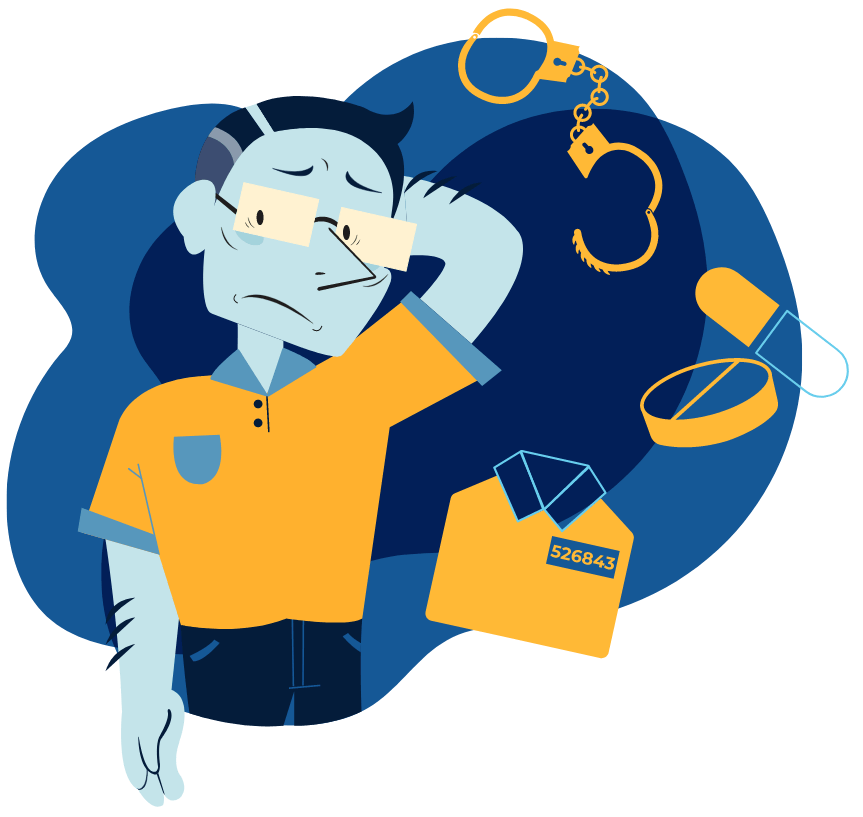
Davie needs a job that will give him a chance.
Davie is a 44-year-old man who has just been released from prison after being convicted of a drug abuse violation. He underwent drug rehabilitation while in prison and is now clean. Having served his sentence, he now lives with a relative and is trying his best to find a job. Davie really wants to be a forklift driver — a job he did before his conviction — but most of the companies in Davie’s location don’t hire recent felons. Although there are many open forklift driver jobs in his area, Davie has had to pivot away from the career of his choice and accept work as a cook at a local restaurant instead.
Davie needs a job that will give him a chance.
Davie is a 44-year-old man who has just been released from prison after being convicted of a drug abuse violation. He underwent drug rehabilitation while in prison and is now clean. Having served his sentence, he now lives with a relative and is trying his best to find a job. Davie really wants to be a forklift driver — a job he did before his conviction — but most of the companies in Davie’s location don’t hire recent felons. Although there are many open forklift driver jobs in his area, Davie has had to pivot away from the career of his choice and accept work as a cook at a local restaurant instead.
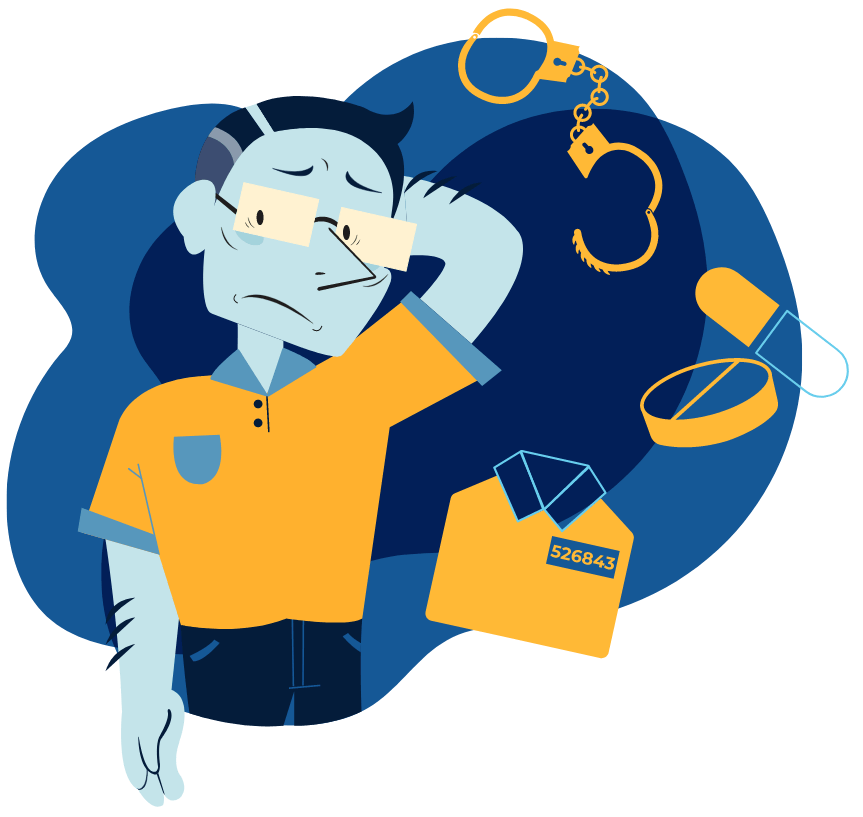
Workers can’t afford health insurance, which means they can’t afford to stay healthy.
Since the 1980s, the number of incarcerated people have soared in the U.S. Today, it is common for an individual to have a conviction record. The reality is, since a large proportion of the American population has an arrest record, employers who create background barriers will miss out on lots of potential talent.
Estimated Number of People Incarcerated (millions)
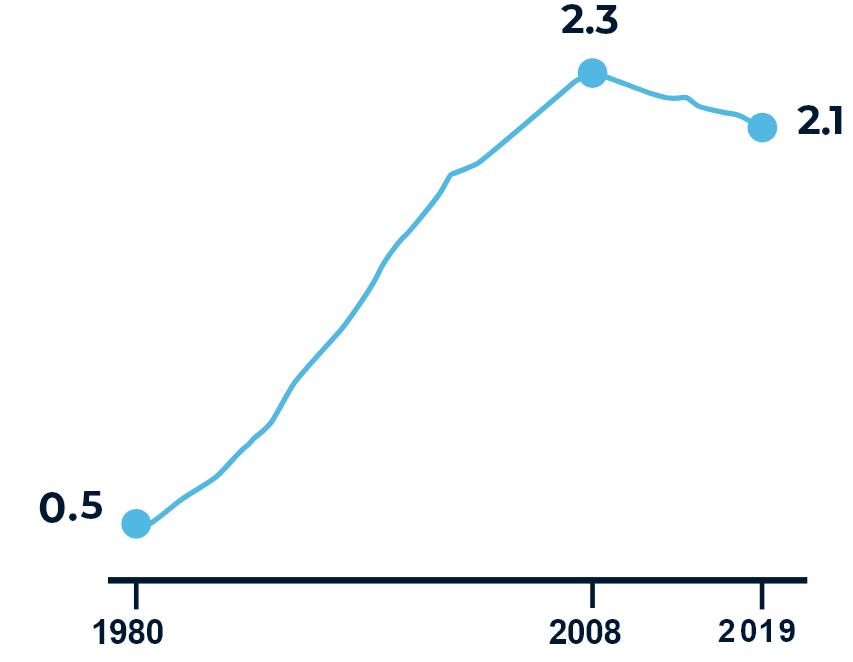
Large Groups of People in America
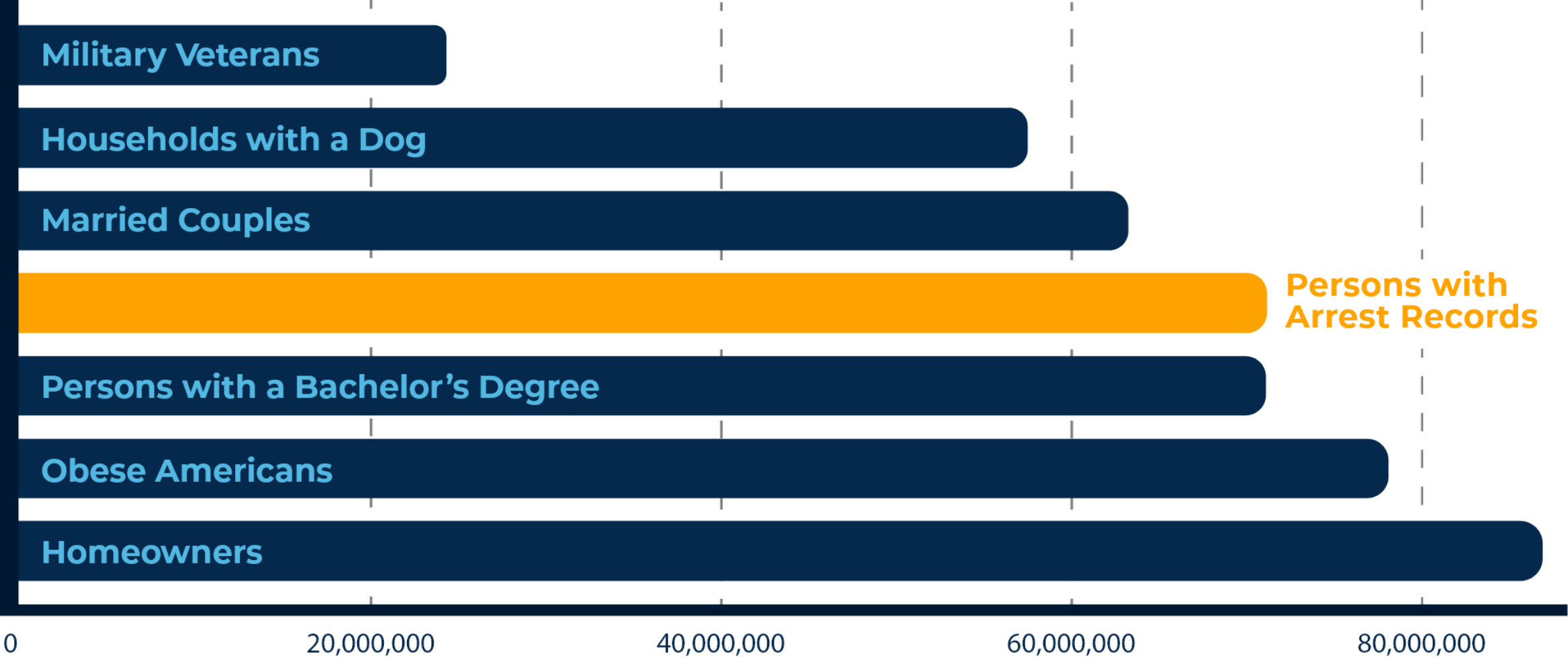
Moving Forward:
Review your hiring process to ensure it is open to a diverse group of talent. Update your hiring policies for the life circumstances of a modern workforce and remove restrictive hiring requirements that aren’t necessary for the job.
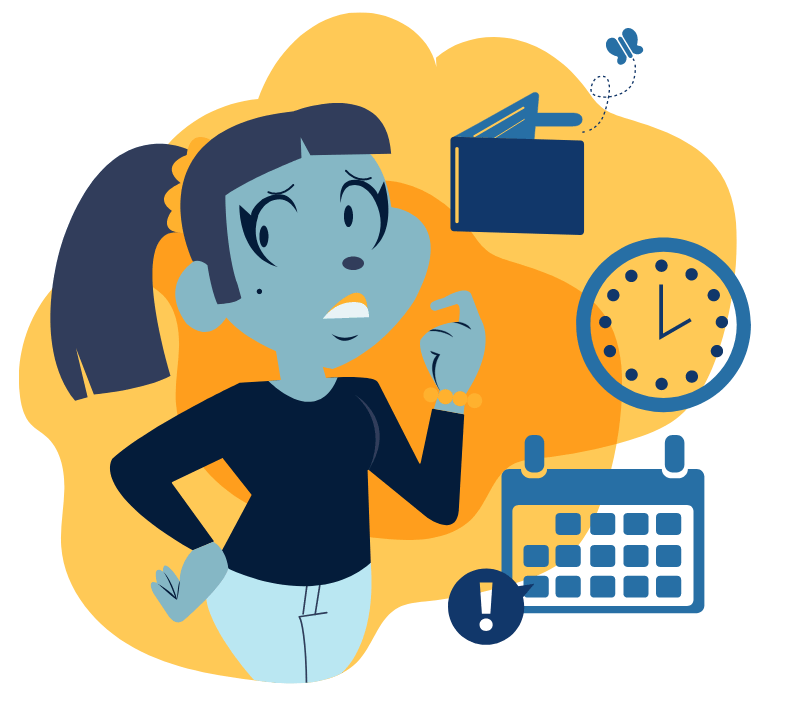
Mia doesn’t have time for a long hiring process.
Mia is a 30-year-old woman who quit a job she couldn’t stand, and now she’s looking for a new position. The thing is, with her current savings, she can only afford to be unemployed for a maximum of two weeks, so she is in a hurry to find her next job. She applies for several jobs, but she has her sights set on a job with a local manufacturing company that is offering good pay and benefits. When she gets an email inviting her to an interview, Mia feels excited, but at the interview, she is informed that the hiring process will take up to 3 weeks. Mia explains that she can’t wait that long without a paycheck, but she is told it is company policy and they can’t make an exception for her. Mia accepts a different job at a local hotel the next day; the hotel took just 48 hours to process her hiring paperwork and get her onboarded to her new position.
Manufacturing has a long hiring process
The manufacturing industry has one of the longest interview processes, but few people, especially those who are low-wage earners in the manufacturing industry, have enough savings to go through a lengthy hiring process without an income. In fact, 56% of Americans don’t even have $1,000 to cover an emergency. In a tight labor market, having a longer-than-average hiring time is a huge disadvantage that will prompt applicants to ditch hard-to-get jobs for more accessible positions.
Moving Forward:
Find ways to reduce the length of your applicant’s time to hire. Eliminate any steps of the process that aren’t absolutely necessary. Get an idea of how long it takes competitors in adjacent industries to hire applicants and try to create a hiring process that beats their time.
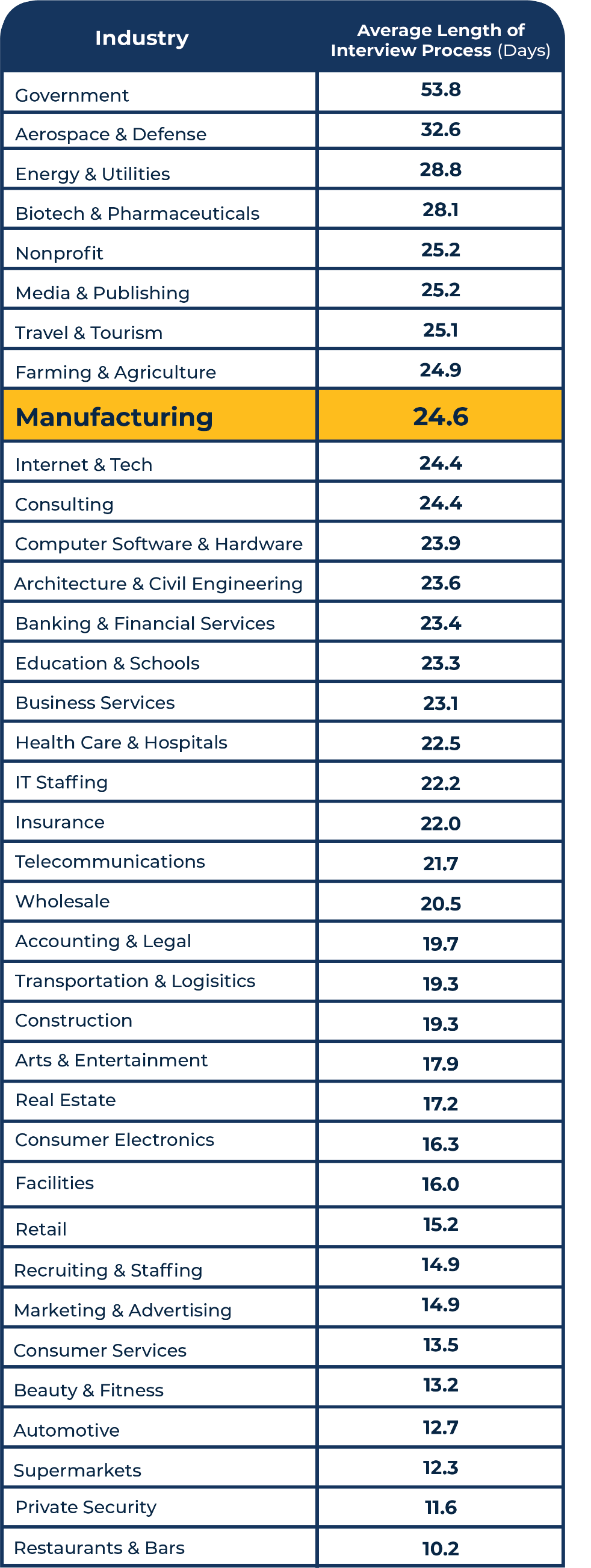
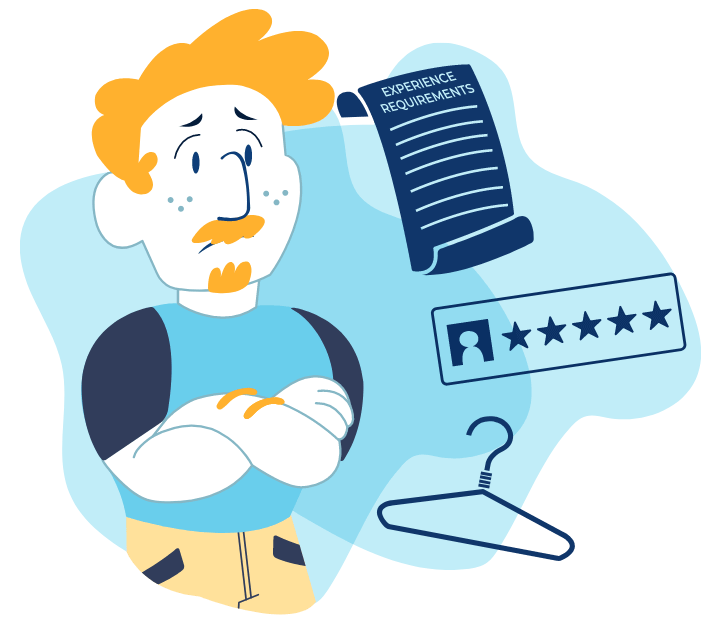
Shawn can’t find a truly entry-level manufacturing job
Shawn is a 28-year-old man who is tired of putting up with angry customers at his retail job. Shawn has worked in retail since high school, and he is ready to switch industries and try something new. He begins to search for entry-level jobs in the manufacturing industry. The problem is, even the jobs labeled “entry-level” require him to have experience in the manufacturing industry, which Shawn doesn’t have, even though he has over a decade of total job experience. Shawn learns quickly and feels he could easily do the jobs if the companies offered training — but since no companies will hire him, Shawn decides manufacturing just isn’t for him. He pivots to a different industry that will give him training and access to a new career.
Shawn can’t find a truly entry-level manufacturing job
Shawn is a 28-year-old man who is tired of putting up with angry customers at his retail job. Shawn has worked in retail since high school, and he is ready to switch industries and try something new. He begins to search for entry-level jobs in the manufacturing industry. The problem is, even the jobs labeled “entry-level” require him to have experience in the manufacturing industry, which Shawn doesn’t have, even though he has over a decade of total job experience. Shawn learns quickly and feels he could easily do the jobs if the companies offered training — but since no companies will hire him, Shawn decides manufacturing just isn’t for him. He pivots to a different industry that will give him training and access to a new career.
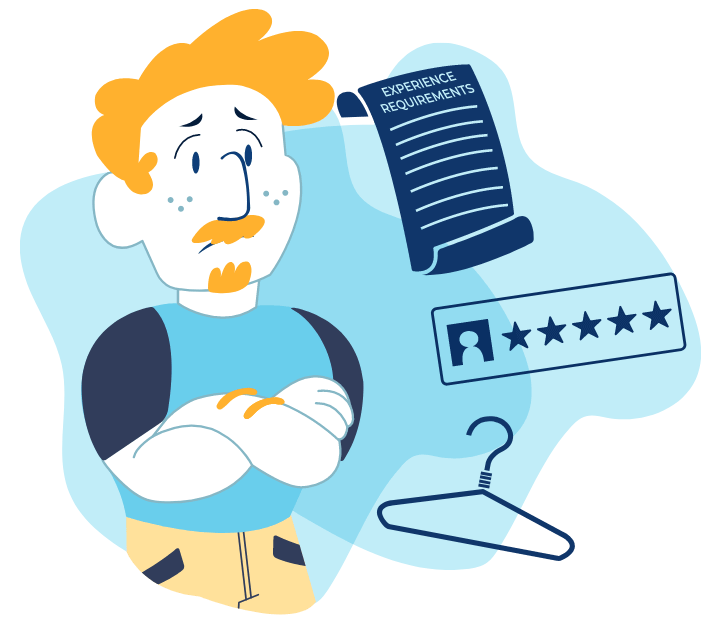
Requiring experience prevents entry-level workers from joining the industry.
Once upon a time, entry-level jobs were for entry-level workers — those who didn’t have any experience. Today, it may actually be more common for entry-level jobs to require experience than to be actually entry-level. That’s the picture a TalentWorks study found, revealing 61% of full-time jobs seeking entry-level employees required at least three years or more of experience.
Manufacturing, specifically, requires the fourth highest amount of experience from entry-level workers, according to a recent Zippia study. Requiring so much experience from workers who will be accepting entry-level pay is a huge detractor for most employees. In today’s tight labor market, employees can easily choose a job that requires less experience and that will provide them with more training opportunities. It’s also important to note that requiring experience, especially on entry-level jobs, limits the pool of potential workers and detracts workers from other industries from making the switch into manufacturing. Inviting new groups of employees to the industry is especially important as the experienced Baby Boomer generation continues to exit the workplace.
Average Amount of Experience Needed for Entry Level Jobs
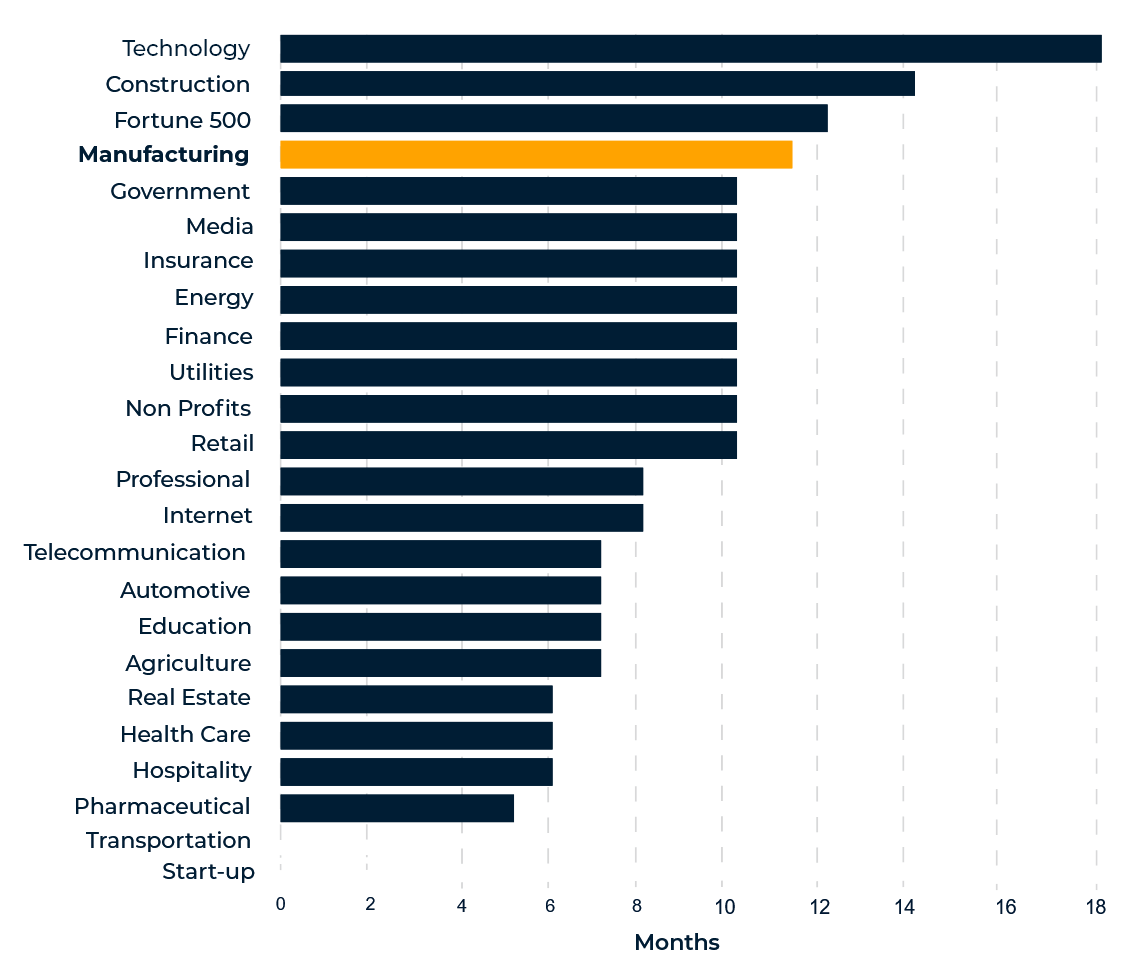
Source: Zippia
Moving Forward:
Consider designing a training program for entry-level workers. Instead of “buying” workers on the market, build your own workforce and create a sustainable pipeline of talent.

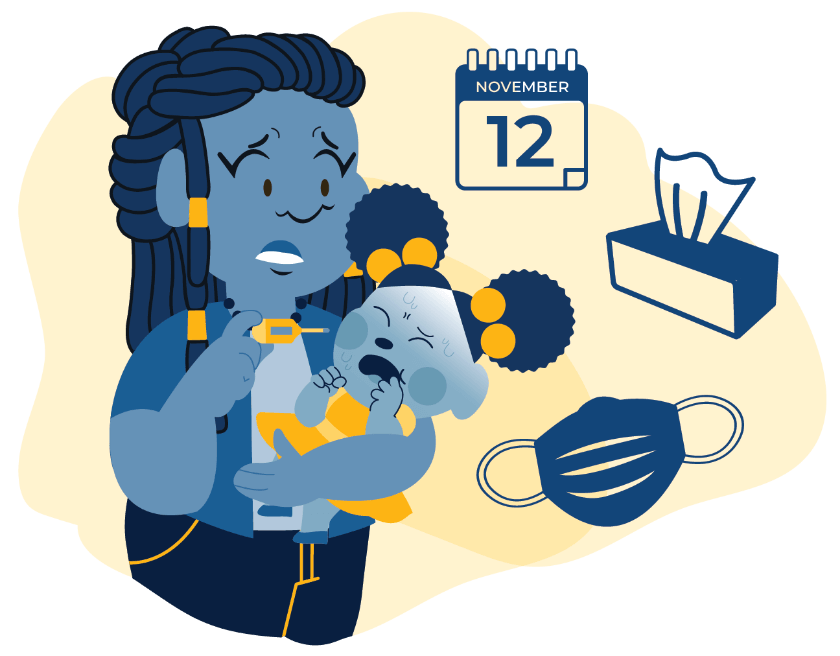
Amber needs flexibility to take care of her child.
Amber is a 24-year-old single mom who just celebrated her two-year-old daughter’s birthday. Before having her daughter, Amber had perfect attendance and prided herself on always showing up. But now, Amber is struggling to find reliable childcare and it has put Amber in violation of her manufacturing job’s policy. Amber’s company gives her two weeks of vacation time to take off, but Amber has already exceeded that number because of her childcare issues. Amber’s daycare intermittently closes during the year during weeks that Amber has to work, which means Amber has to take off more vacation days than she has. What’s more, every time her daughter runs a fever at daycare, Amber has to leave work early — oftentimes in the middle of a shift — to pick up her daughter. Since the covid outbreak began, local daycares are only getting more unreliable. Amber’s employer terminates her for violating their attendance policy. Amber is devastated. Instead of looking for a job in her field, she decides to work at a local restaurant that is offering flexible shifts.
Traditional manufacturing schedules don’t work for many parents
The U.S. Has the world’s highest rate of children living with a single parent, with almost a quarter of u. S. Children living in a single-parent home, according to a recent pew study. This actually has major repercussions for today’s employers, especially those in the manufacturing industry, whose employees tend to trend younger and are therefore more likely to be parents of young children.
Manufacturing jobs are known for having traditionally rigid shift schedules and strict attendance policies, which often aren’t suited for parents of young children. Single parents often shoulder the huge responsibility of parenting with limited help. As a result, many parents require a lot of flexibility to deal with the unpredictable needs of their children and personal lives. After all, young children often require immediate, hands-on attention with little notice. What’s more, many parents do not have access to adequate child care, which makes it even more difficult for parents to join the manufacturing industry without flexible schedule options.
Moving Forward:
Consider creating a more flexible schedule for workers. Possible solutions could include a no pay no penalty program, allowing workers to choose their shifts ahead of time and eliminating strict attendance policies that would penalize parents. It may likewise be helpful to understand the schedules of local schools in your area and ensure your work schedule is not misaligned with the school schedule.
Number of People in Childcare Deserts, by Urbanicity (millions)
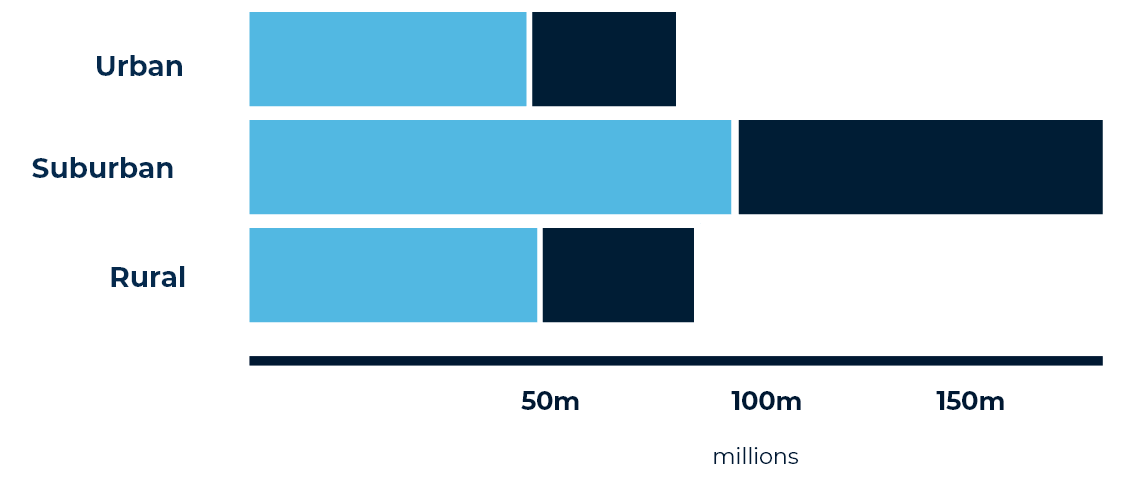
Share of People in Childcare Deserts, by Income
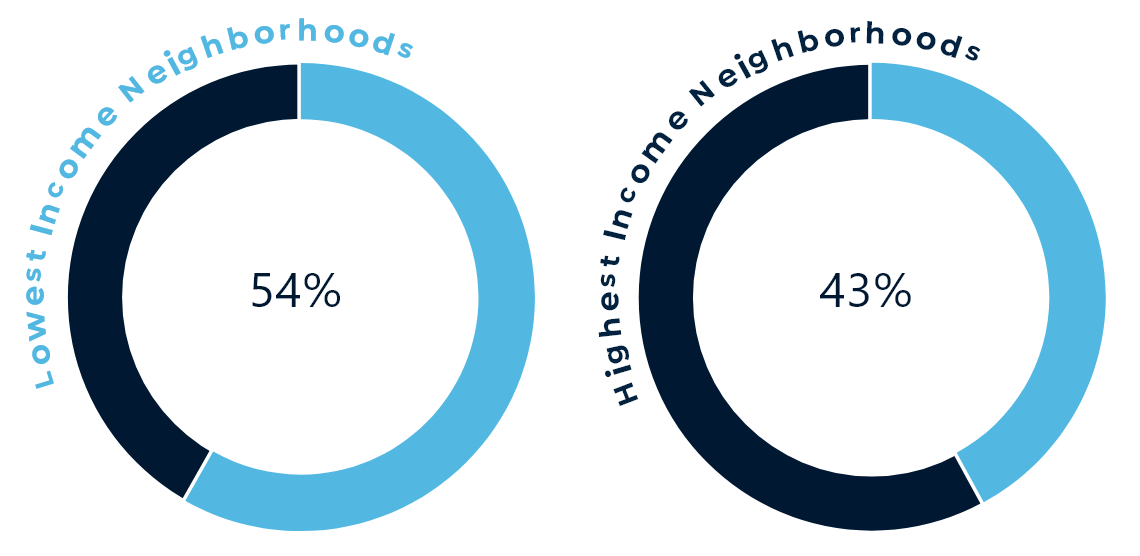
Number of Children with a Single Mother or Father in the U.S.
Source: Statista
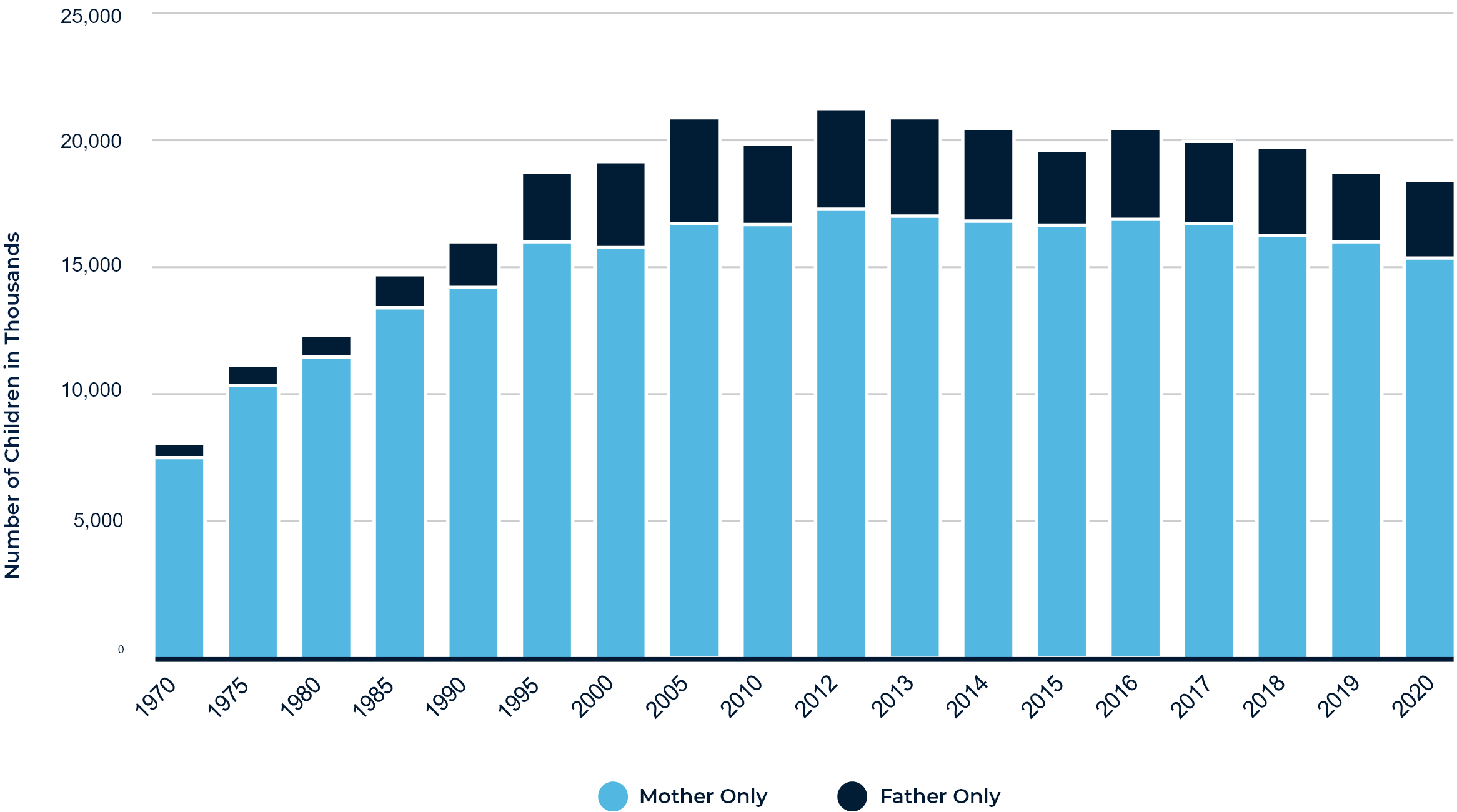
The Way Forward
Right now, it is difficult to recruit and retain employees in the manufacturing industry. We are seeing historic numbers of open jobs and quit rates. The thing is, those historic numbers didn’t just appear. America’s workers — and their needs — have been evolving over the past couple of decades. In addition, the pandemic has escalated many workers’ needs and has created some new barriers to employment. Ultimately, the modern worker requires different kinds of accommodations from employers to succeed in the manufacturing industry. In order to recruit and retain workers, we must first understand what modern employees require and desire from their jobs in a rapidly changing world. For many companies, today’s workforce instability is a wake-up call that it is time to innovate and reconsider the kind of future we would like to build with our workforce.
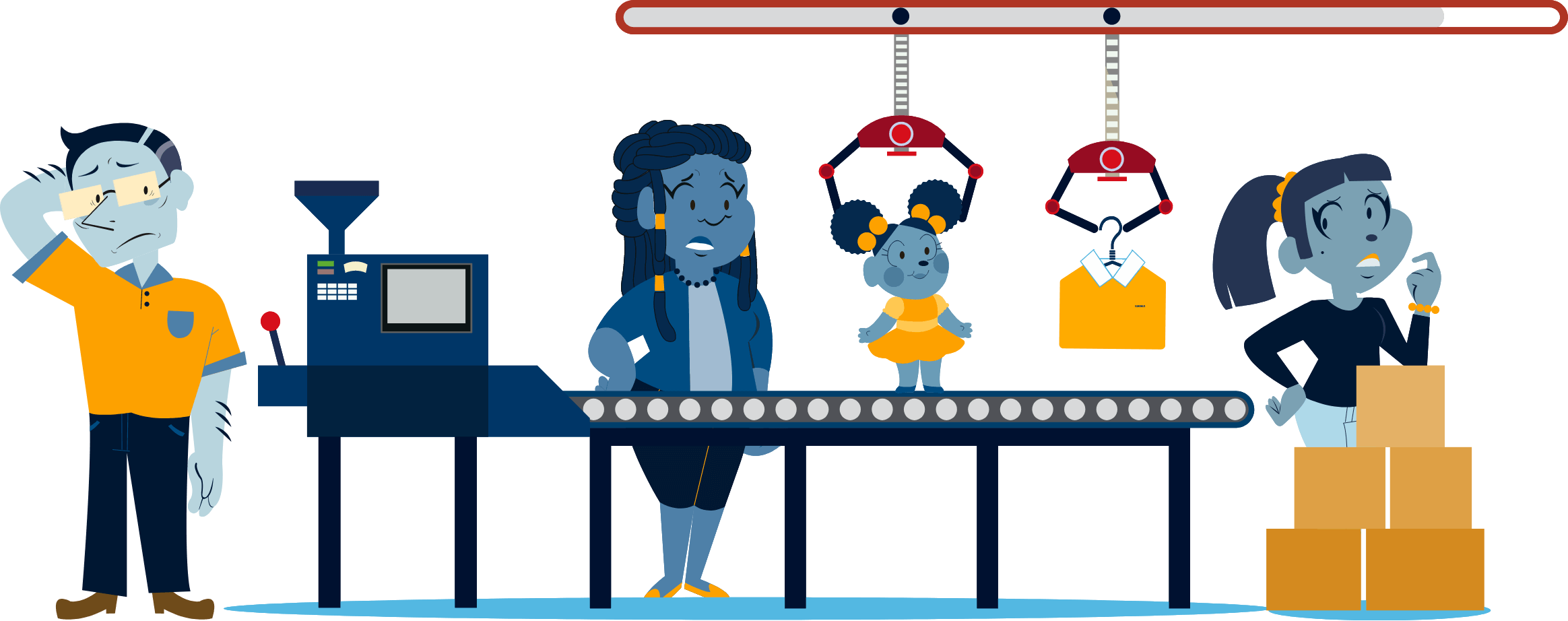